Management matters: Switch to new farrowing system cuts labour cost
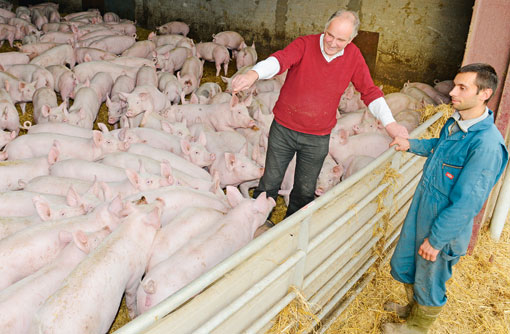
The average pig producer has failed to make a profit for at least two years and the Strathmore Farming Company is no different, with the average loss per finished pig running at £5.
Despite this, farms manager David Soutar says he is firmly committed to pigs on the 2,482ha enterprise, with no immediate plans to exit the industry. His only hope, however, is that the DAPP (deadweight adjusted pig price) reaches at least cost of production soon, presently 173p/kg.
“It’s a great disappointment that DAPP has not gone forward as everyone had expected and it is still way off the true cost of production,” says Mr Soutar.
“However, pig production is at an all-time high, which is reducing fixed costs but increasing losses on finishers, with more pigs to stuff expensive feed into.”
He says physical performance on the unit has never been better – 22 pigs from every sow are finished and sold at 80kg liveweight every year, equating to approximately 1.7t pigmeat a sow a year.
“As a business, it’s critical that we sell as many kilograms of pigmeat a week as possible. Generally the industry has reduced weights, but from our point of view we need kilograms to make money,” adds Mr Soutar.
He says assistant farms manager Alastair Adams and the pig team are working hard to keep costs to a minimum and output up. “Both are needed if the long-term prosperity of the unit and the eight jobs it supports are to be maintained.”
A key area he thinks needs improving is the premium paid to Freedom Foods producers.
“We really like being part of Freedom Foods, but we don’t get enough from the processors for it. When the pig price was 100p/kg, we were getting an 8% premium, but now we are getting less than 5% premium,” he says.
Radial farrowing system
Although feed costs cannot be altered and finishing remains an expensive business, sow costs can be reduced and it is hoped a new radial farrowing system (see opposite) – based on a concept developed by Dent Ltd of Yorkshire – will reduce labour costs.
“We are trialling a system of farrowing field set-up which was developed by Dent, which we hope will improve cost of weaning and life balance for staff. Instead of picking up the piglets individually, we gather them all up like sheep in a pen and then take them from their mother,” says Mr Soutar.
“Up until now, when our guys were weaning, they were starting at 3am and the hope is that we can reduce four hours of weaning labour from each person – that’s 16 hours every three weeks.”
The key to future business profitability is finding innovative alternatives to current management practices in outdoor production, to get production up and costs down, he adds.
One idea to help improve efficiency is the introduction of a new feeding system for dry sows. But this will require substantial investment and until the average DAPP improves, it’s not an option, says Mr Soutar.
However, the most dramatic influence must come from better farrowing production and this is where the focus lies, with trials of a new type of farrowing hut proving exciting.
Slaughter outlet
Following the closure of the Vion Hall’s of Broxburn plant, pigs are now being sent for slaughter to Malton, North Yorkshire – the base of the newly named Karro Food Group (former Vion pork enterprise, which was bought out by management earlier this year).
“The management buyout of the pork site at Vion is probably the best result we could have because it’s keeping that business focused on pork,” says Mr Soutar.
The new arrangement involves a longer travelling time for the pigs and more expensive haulage costs (partially subsidised by the processor). The new longer haul to Malton costs £1,250 for every batch of 200 pigs, compared to £440 when they were going to Hall’s.
However, despite this being far from an ideal arrangement, Mr Soutar says he is happy so long as the extra payments to help with haulage costs continue and the animals are not suffering from it.
“Latterly, we were putting pigs into Hall’s at 2pm but for a while we were having to put them in the night before and they were losing more weight in the lairage than when they are in the lorry overnight to Malton.
“If they had gone in the evening and spent the night in a lairage to be slaughtered in the morning, they would have been more upset, but they seem happier in the lorry which eases my concerns about the longer journey.
“However it would be preferable if we could have them all contract killed in Scotland.”
In addition to supplying Karro Foods, a number of pigs are supplied to a wholesale butcher in Glasgow and a new arrangement with prestigious caterers Wild Thyme, which now runs the restaurant at Glamis Castle on the estate, will hopefully lead to more pigs being consumed through this tourist outlet.
Aftermath of 2012
Staff commitment and determination has been key to maintaining production and surviving the horrendous weather of 2012, says Mr Soutar.
“Dedicated staff, both on arable and livestock, generally were key to 2012 because they have had to cope with the most hellish weather and it’s only due to their resilience and determination to make it work that we keep on producing results,” he says.
He describes 2012 as the wettest and greyest year in the past 25 years, with the worst floods seen on the farm in more than 30 years.
Despite this, the team managed to get in a reasonable crop of straw – 50% more than in 2011 – which will be used on the pig finishing units, thus reducing costs compared with 2011.
“The price of grain has compensated for lower yields to a degree but costs of harvest and drying were through the roof,” adds Mr Soutar.
“However, we do have to sell grain in conjunction with buying pig feed as we don’t want to get caught in the worst-case scenario of selling grain and buying feed at the wrong time.”
He describes a poor harvest in 2012 and higher losses in the pig enterprise as a “double whammy” in terms of stresses on cashflow.
“Managing cash flow was tricky for a few weeks with a late harvest coinciding with peak losses on pigs and never before was our single farm payment, in euros, so welcome,” says Mr Soutar.
“With the help of Berkley Futures, we managed to do better than had we opted to take sterling. A few cash-and-carry deals on stored grain helped, and I am pleased to say that with much reduced losses on pigs, this situation is now nicely reversed.”
Find out more about the Strathmore Farming Company and view a video with David explaining how the enterprise works