Graham Hayllar’s custom umbilical slurry pumping trailer
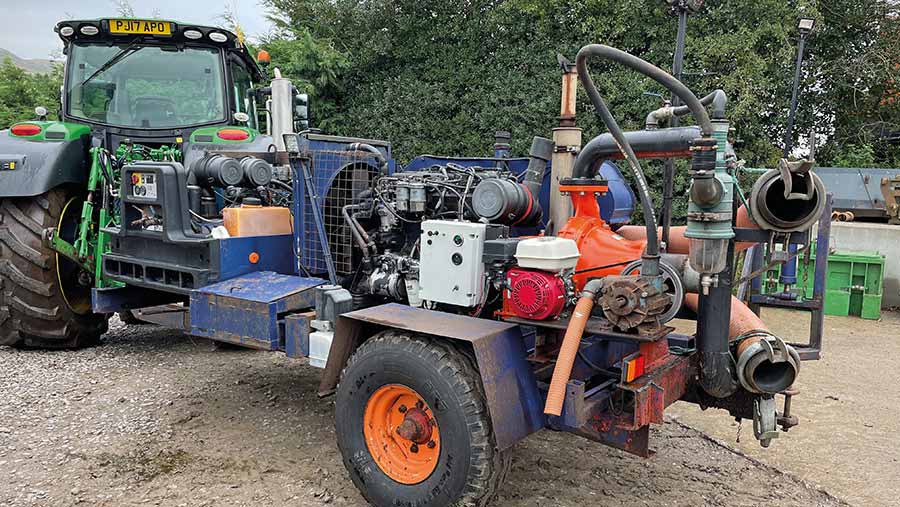
Cumbrian contractor and agricultural engineer Graham Hayllar built his first slurry pumping trailer more than 25 years ago and has since added two more to his fleet.
The idea for his first rig came soon after he got into umbilical spreading. His original off-the-shelf kit consisted of little more than a centrifugal pump mounted on a wibbly three-leg stand, a reel of pipe and a splash plate.
It worked after a fashion, but it was tedious to move around and there was no way of cleaning out the pipes, other than running over them with a tractor wheel.
See also: What’s in Your Shed? visits a Cumbrian contractor
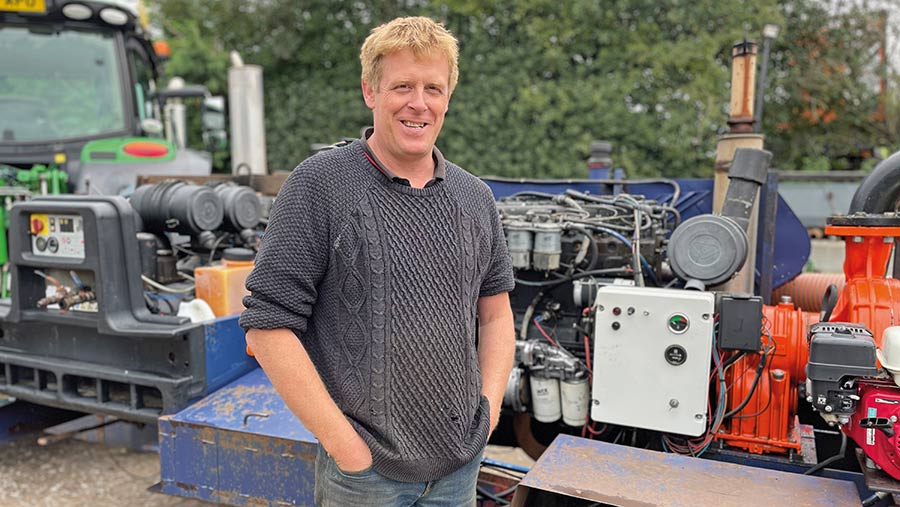
Graham Hayllar © James Andrews
Mr Hayllar soon came up with the idea of building a trailer to carry the pump and suction pipes, as well as a pto-driven compressor to blow out at the end of the job.
Switching between running the pump and compressor simply involved taking the tractor pto off one and moving it onto the other.
Not long after, he built a second trailer, this time using an old self-propelled road compressor, which negated the need to move the pto.
Together, these rigs transformed his slurry operation, but they still required a tractor to be hooked on the front clocking up hours.
To take the strain off the tractors and free them up for other jobs such as stirring, he set about making a self-propelled unit.
Going self-propelled
The engine was the starting point, which came in the form of a 150hp Perkins six-cylinder from an old combine that he picked up for £1,200.
This came complete with the radiator and fuel tank, so he just had to fashion a frame to hold it and sort out the wiring and gauges.
Another key element was the pump. Mr Hayllar had already seen good results with the Cri-man units he had used on his other pumps and, through the engineering side of his business, he has also started selling them
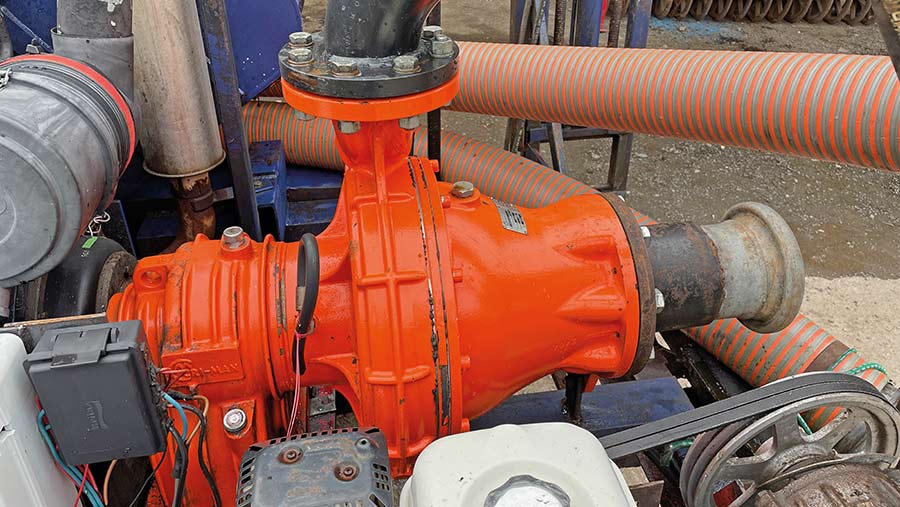
Drive to the Cri-man pump runs through a gearbox © James Andrews
Rather than use a direct drive from flywheel to impeller and rev the engine hard to get the required speed, he opted for a unit with a built-in gearbox.
The two are connected using a Fenner flexible coupling to take out any vibrations in the driveline.
To accommodate the various elements, Mr Hayllar and his team built a custom channel and box-section chassis, which runs on a single axle.
The engine and pump assembly are located at the rear, leaving room for a second-hand CompAir portable compressor to be transverse mounted at the front
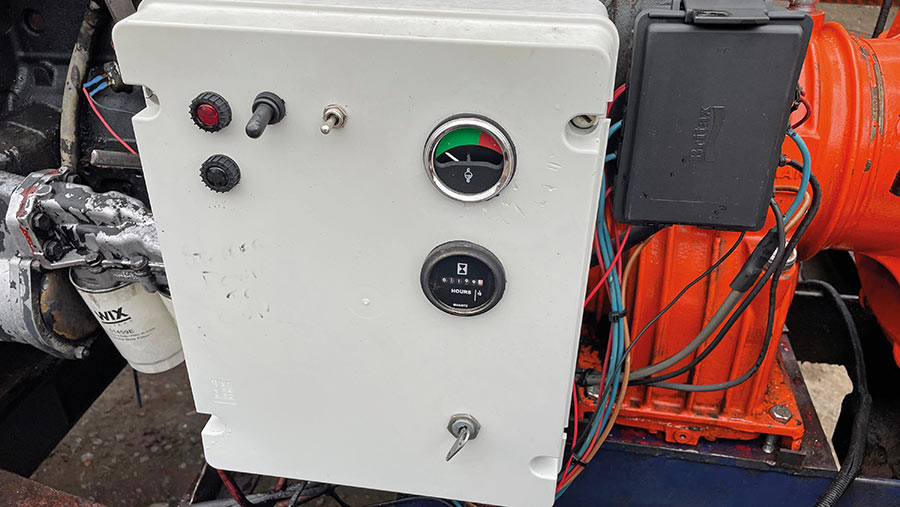
Engine controls are housed in a box above the axle © James Andrews
At the side, they also made room to stow a couple of suction pipes. These are typically one male-to-male, and one male-to-female, which allow them to work with most farm setups.
Priming of the main pump is handled by a 5.5hp Honda engine that powers an old milking machine vacuum pump.
This is run until slurry appears in a sight glass in the pipe run, telling the operator that there is enough drawn through to get it going.
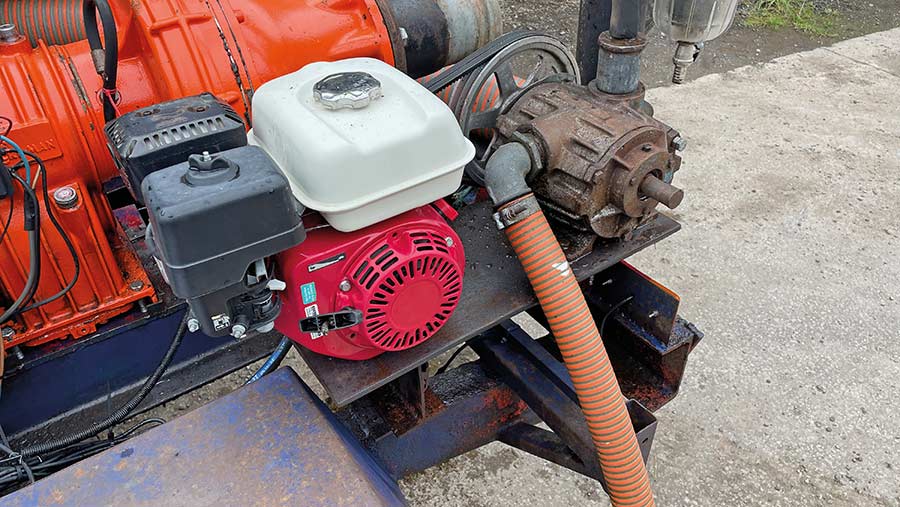
© James Andrews
Alternatively, they also have a venturi primer that can be inserted into the pipework to draw slurry through the pump using the compressor.
The final part of the setup is a hydraulic pipe clamp that is used in place of a gate valve to control the flow of slurry.
This runs off an electro-hydraulic unit – as used on tipper trailers – allowing the operator to lower and raise the clamp without having to run the engine.
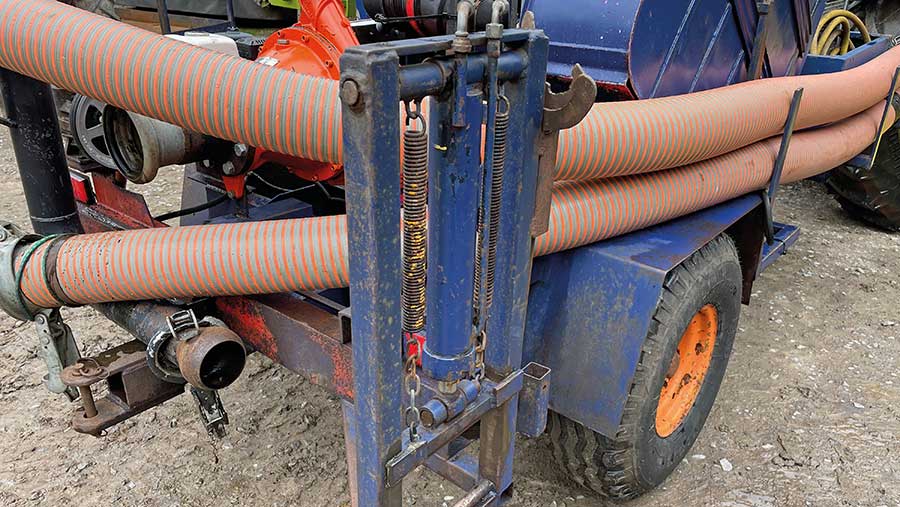
© James Andrews
Each side of the clamp is formed out of smooth steel bar to reduce the risk of damaging the pipe but, for added protection, they’ve included an extra sleeve on the section that gets nipped.
The total price of the build was about £8,000, most of which was for equipment that would still be needed with a tractor-driven setup.
“It’s really only the cost of the engine and steel for the trailer that’s extra, so it was a cheap build that has paid for itself several times over,” says Mr Hayllar.
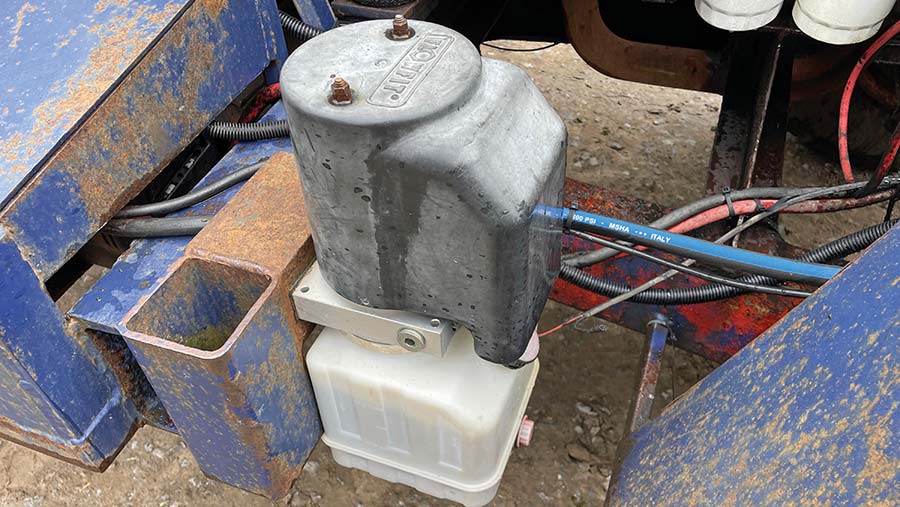
© James Andrews
Using it
Most of the farms the team visits will require the lagoon or tower store to be stirred before pumping, so one tractor will tow the pumping rig and a stirrer to the site.
All of Mr Hayllar’s pumping trailers have hitches on the rear allowing other equipment to be towed behind, and both his tower and lagoon stirrers have been modified so they run on their own trailers.
Once set up, the driver can run the pumping trailer and stirrer simultaneously, flitting between the two as required.
Splash plate is still the most popular method of application in the area, but increasing numbers of customers are opting for dribble bars. Mr Hayllar runs both 9m and 12m units from Agquip.
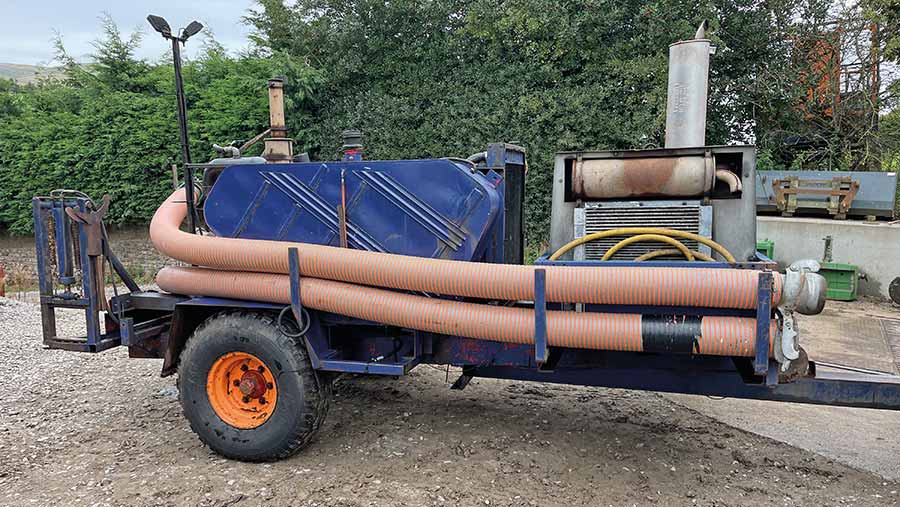
© James Andrews
Thanks to the gearbox on the pump, the Perkins engine can generally be run at 1,500-1,800rpm, meaning it uses 30-40% less fuel than one of his tractors.
In an average year, the pump will work for about 1,000 hours, which soaks up a good chunk of depreciation.
On its own, the self-propelled trailer can serve up to 2,000m of pipe, which means there is rarely a need for double pumping.
More often, the team will have two pumps and splash plates/dribble bars running off the same lagoon to increase output.
In this instance, a second remote-controlled trailer would come in handy, making it easier for one operator to run both pumps.
Remote-controlled trailer
Parts are already being assembled for one of these, including a 220hp Mercedes V6 previously employed on a Claas forager that was sourced from Lancashire breaker David Cowking.
Mr Hayllar opted for the extra power as the 150hp Perkins on his current rig is pushed hard when working on longer runs.
“The V6 will have more than enough power for the job, so hopefully we’ll be able to use it at even lower revs, and maybe use less fuel,” he says.
This will be teamed with the same Cri-man pump as his other trailers, and he has bought another CompAir compressor to go with it.
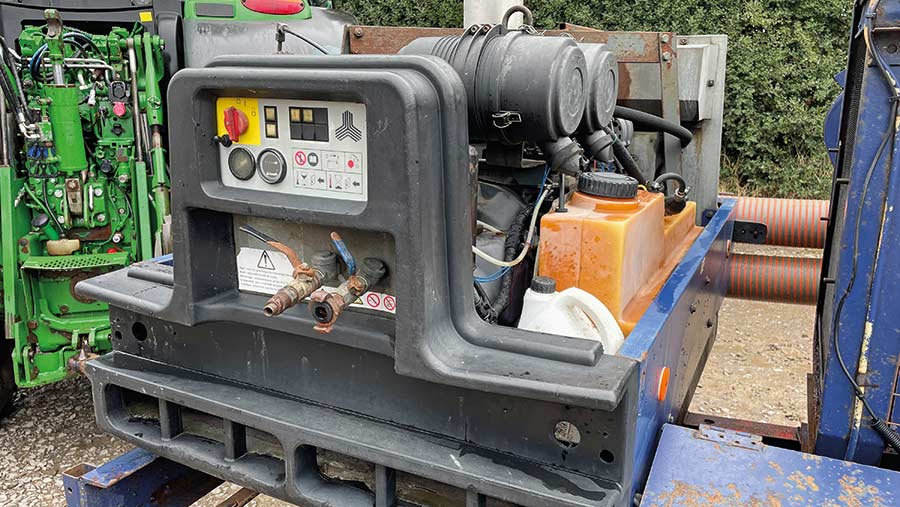
The CompAir portable compressor is mounted transversely at the front of the trailer © James Andrews
He has various remote-control options to choose from, but is favouring a setup from Lancashire firm Raw Equipment.
This will give the option of starting and stopping the engine, adjusting the revs, diverting the flow of slurry back to the store and starting/stopping the compressor.
Nurse tank
Another recent project has been the construction of a 55cu m nurse tank that allows umbilical spreading to be carried out at remote blocks of land.
It was built from scratch using a braced box-section frame clad with 5mm sheet steel.
This sits on a lorry trailer axle with a hydraulic raise and lower system, allowing it to be towed to site and then dropped flat on the deck.
This is essential, as it holds about 55t worth of slurry.
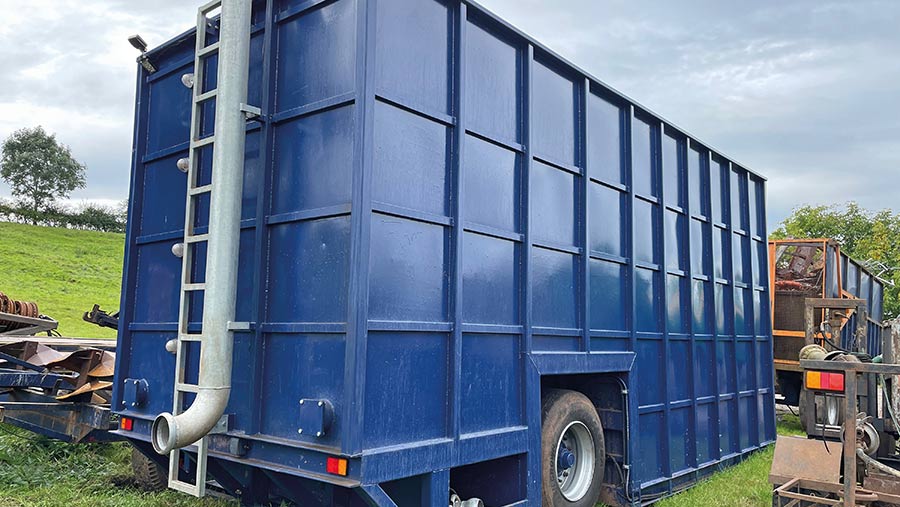
A home-made 55cu m nurse tank allows for umbilical spreading on remote blocks of land © James Andrews
Tankers can blow into it using a pipe that runs up the side and empties into the top.
When the level is high enough, the built-in pto-driven Cri-man pump is able to self-prime and send the liquid directly to the splash plate or dribble bar.
Alternatively, the self-propelled pumping trailer can be connected to an outlet, saving a tractor sitting there revving away.
Built-in sight glasses at both the front and rear make it easy to keep an eye on the level, but there is also an inspection ladder to get a view in over the top.
G Hayllar’s self-propelled pumping trailer
- Engine 150hp Perkins six-cylinder
- Pump Cri-man
- Compressor CompAir
- Priming setup 5.5hp Honda engine with milking machine vacuum pump
- Flow control Custom-made hydraulic pipe clamp
- Build cost £8,000