How to build a Johnson-Su bioreactor to produce your own on-farm biology
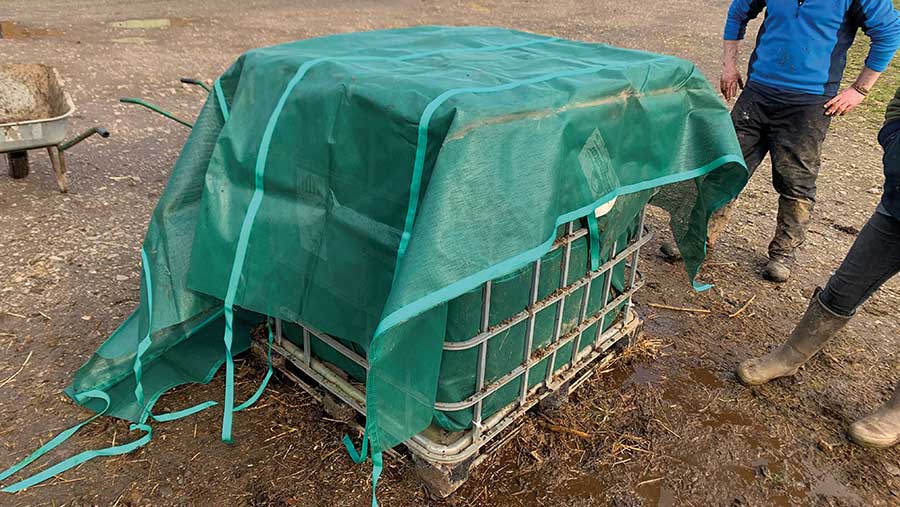
Building biology on your farm doesn’t need to cost the earth, although it does require a level of patience.
There is more than one way to increase microbial activity in soils, but a method gaining momentum with farmers focusing on regenerative principles is applying a microbial inoculant made using a Johnson-Su bioreactor.
David Johnson, adjunct professor at California State University’s Center for Regenerative Agriculture and Resilient Systems, and his wife, Hui-Chun Su carried out research into biological soil enhancements for the Institute of Sustainable Agriculture at New Mexico State University.
They created the system to produce a fungal-rich compost that can be used as a microbial inoculant.
See also: The Soil Health Scorecard: What it is and how to use it
The aim was to mimic what happens to dung and organic matter on prairies in a system that doesn’t require farmers to have grazing animals on farm.
Results in the US from applying the resulting compost as an extract in farm-scale maize trials matched the productivity of conventional systems using just 15% of the applied nitrogen.
Those types of results have attracted the interest of UK growers and advisers, including Sustainable Soil Management’s Ian Robertson.
His firm offers help and advice to farmers who want to produce Johnson-Su compost in a home-made bioreactor.
Making a Johnson-Su bioreactor should only take a couple of hours, using easily sourced, cheap materials. It’s a five-step process, he says.
What you need to make a Johnson-Su bioreactor
- 1,000 litre IBC with plastic pallet
- Galebreaker (or similar) landscaping mesh
- Drainage pipes – about 10-12cm diameter
- Hose pipe for an irrigation system
- Cable ties
- Raw materials to fill the bioreactor
1. Line the cage from an IBC
The starting point is a caged 1,000-litre IBC connected to a plastic or non-rotting pallet, Mr Robertson says. A wooden pallet is at risk from rotting from microbial action.
Remove the top bars of the IBC and take out the plastic container. “It’s the cage you’re after,” he says.
The cage is lined with Galebreaker mesh to create a basket, using cable ties to fix it in firmly in place.
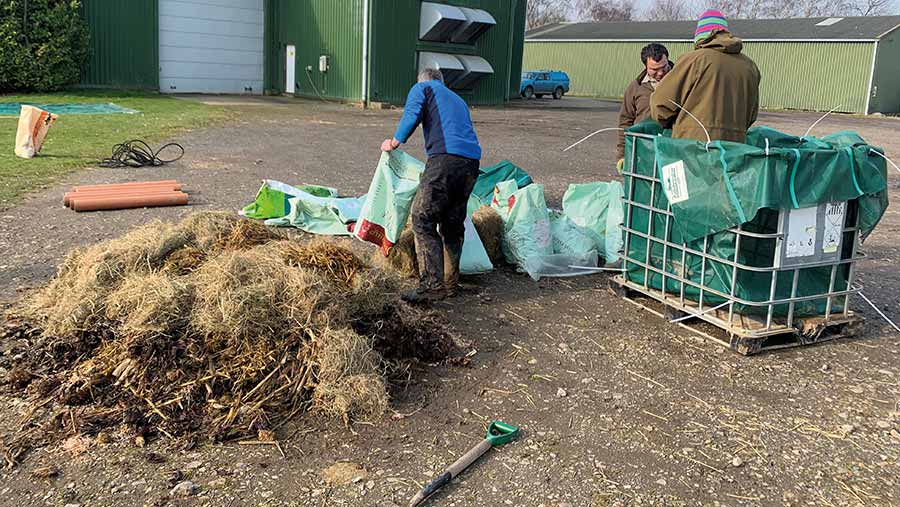
Lining the cage © Ian Robertson
2. Position drainage pipes
A key requirement for making Johnson-Su compost is that it must be aerobic.
The Galebreaker lining ensures air flows from the outside, but the aim is for no part of the compost to be more than 30cm from air.
To achieve that, drainage pipes are temporarily placed inside the lined cage to create air flow through the bioreactor.
These should be cut to a length that will sit about 15cm above the rim of the cage.
Drill holes in the pipes at the top for fixing in place, and down the length, approximately 15cm apart on four sides, to allow more air flow while they are still in place, suggests Mr Robertson.
Put the IBC top bars back in the cage, and use them to position the pipes in two rows of three, about 30cm apart. Cable-tie the pipes so they remain in place while filling the bioreactor.
Once ready to fill, stuff an old sack in the top of each pipe to prevent any composting material going in the pipe rather than the container.
Site the empty bioreactor near a water supply, ideally under cover in an airy shed.
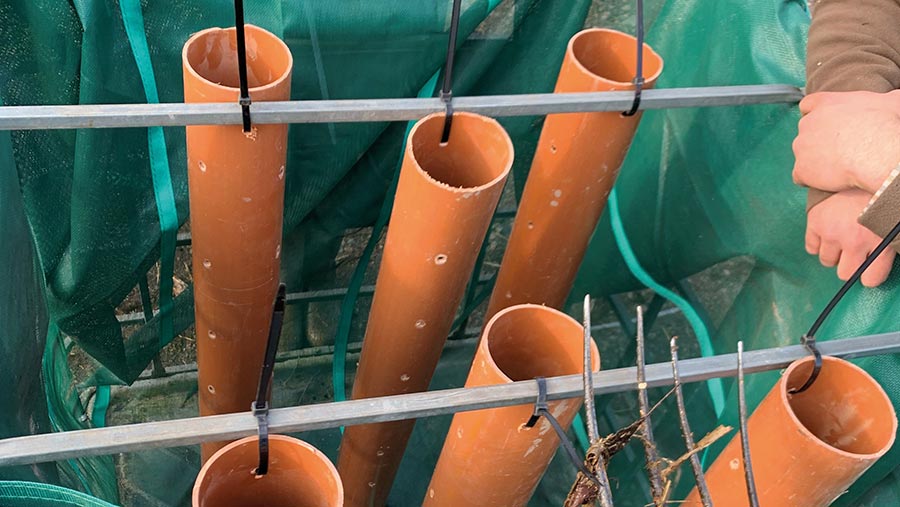
Positioning draining pipes © Ian Robertson
3. Prepare the composting materials
There is no set recipe for the raw materials for the compost, although the aim is to have a mix that has a 25:1 carbon:nitrogen ratio, says Mr Robertson.
His suggested starting point would be 25% farmyard manure, preferably from cattle or chickens, 25% hay or other dried green material, 25% fresh green material such as grass clippings or forage crop, and 25% chopped maize.
Other possible raw materials include straw, horse manure or leaf mulch, he says.
The material needs to be four things:
- Chopped or shredded to increase surface area – through a silage or forage chopper is ideal
- Local – don’t buy it in from miles away. Ask neighbours if you don’t have it on farm
- Damp, but not soaking wet. Either mix with some water, spray with a hose pipe or leave outside for rain
- Mixed
The easiest way to fill is using a front loader, although a more manual fork or shovel can be used. Typically, you will need about 1.5cu m of material to fill a 1cu m IBC, he reckons.
“Some won’t agree, but we find it can be worth standing on the material in the bioreactor when filling. You don’t want to compact it because it will go anaerobic, but otherwise it can be too fluffy and shrink a mile once it settles.”
4. Connect the sprinkler system and remove pipes
One prerequisite for making an effective Johnson-Su compost is to keep the mix at about or just above 70% moisture content to keep the microbes happy.
Much less water will need to be added in the UK than in New Mexico, but some form of irrigation system is useful.
Mr Robertson suggests a leaky hose or drip-irrigation system connected to the water supply is ideal.
“You don’t want water running out of the bottom. Check whether it is damp just under the surface to see if it needs water.”
A soil moisture gauge can also be useful to measure different parts of the pile.
Covering the top with more mesh will help conserve some moisture loss. In damp, cooler weather you are unlikely to need to add water much, while in hot periods over summer it might be once a week.
After about a week, once the pile has settled, remove the drainage pipes to improve airflow through the bioreactor.
The holes created should maintain their integrity over time, but if required, use a stick or bar to reopen them.
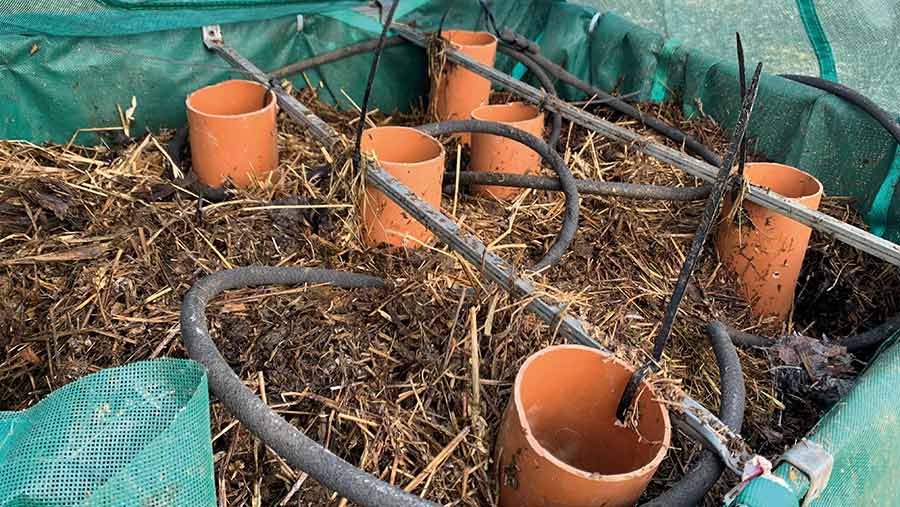
Sprinkler system © Ian Robertson
5. Add worms
As composting begins, the temperature will rise to 60-70C before falling. Once it is below 30C, introduce earthworms to help with the process.
“Ideally, these should be found locally – you need about 40-50 – preferably a mix with some epigeic surface dwellers.”
This is when the requirement for patience kicks in – composting takes about a year to 400 days to complete.
“By the end it will have shrunk down, so you might only have 60cm of a concentrated, soil-like putty at the bottom.”
The end product should be microbially diverse and active, he says. “Have a look under a microscope or send it away to be analysed.”
Analysis comparing a farmer’s field with his Johnson-Su compost showed a massive increase in microbial activity (see “Comparison of field soil and Johnson-Su compost after six months”) just halfway through the process, he says.
“We’re looking for diversity – to grow things that we’re missing in the soil in the field. That’s usually your third trophic level, such as protozoa.”
Most agricultural soils are bacteria-dominated, he explains. Protozoa predate on bacteria and help cycle food that fungi or plants use, keeping the soil food web functioning.
Comparison of field soil and Johnson-Su compost after six months |
||
|
Soil |
Johnson-Su compost |
Microbial biomass (mg PLFA/kg) |
14 |
290 |
Total bacteria (mg PLFA/kg) |
14 |
170 |
Total fungi (mg PLFA/kg) |
1.7 |
90 |
Protozoa (mg PLFA/kg) |
0.11 |
9.0 |
Fungi:bacteria ratio |
1.0 |
2.7 |
Note: Phospholipid-derived fatty acids (PLFA) are used as a proxy to measure microbial biomass |
What to do with mature Johnson-Su compost?
Most users of Johnson-Su compost make it into a compost tea – water in which the compost has been steeped.
Microbes and nutrients leach into the liquid and can then be applied to soil, Ian Robertson says.
“Put it into a muslin bag and then bubble in water to extract the goodies,” he says.
He works on about 10kg of material in 1,000 litres of water to make the compost tea, which is applied as a spray or through dribble bars at 25 litres/ha to cover about 40ha.
“It’s not an exact science,” he admits. “How to apply the inoculant for the best effect still needs a lot more research in the UK.”
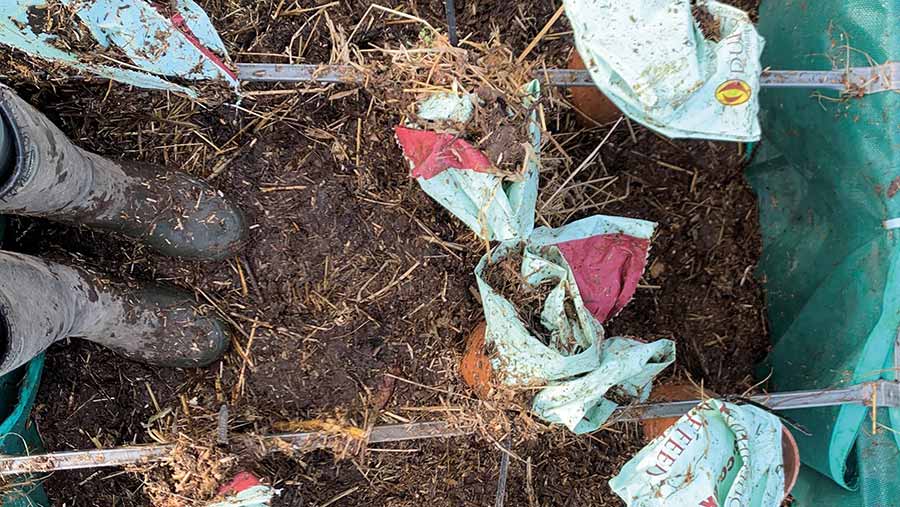
View from above the bioreactor © Ian Robertson
Current advice is to apply at drilling, or potentially as a rip-and-drip application down the leg of a cultivator with molasses, fish hydrolysate and water.
“Another known application method is to use the finished compost and mix it with seed as a seed dressing,” he says.
The evidence of the benefits of using Johnson-Su compost in the UK is so far very limited.
Most of the dozen farms Mr Robertson has been involved with will only be using the finished product for the first time this autumn.
“The staggering difference in phospholipid fatty acids analysis results are measurable. The big question is what that is going to do to my field and farm this year.
“But this is low-cost biology that takes a few hours to set up.
“Biology is ubiquitous if we make the right environment for it. The aim is to kick-start the soil’s food web, and get diversity back on farm.
“It’s important to recognise that Johnson-Su is not the answer on its own – it’s part of a system and one stage of trying to increase diversity on farm,” he concludes.
Case study: Andrew Jackson, Scunthorpe, Lincolnshire
North Lincolnshire grower Andrew Jackson’s interest in producing Johnson-Su compost began after hearing David Johnson speak at the National No-till Conference in January 2020 in St Louis.
“His results were convincing – increasing yields by 1.5 times or more. It seemed to be such a cheap option for making compost that there was little to lose.”
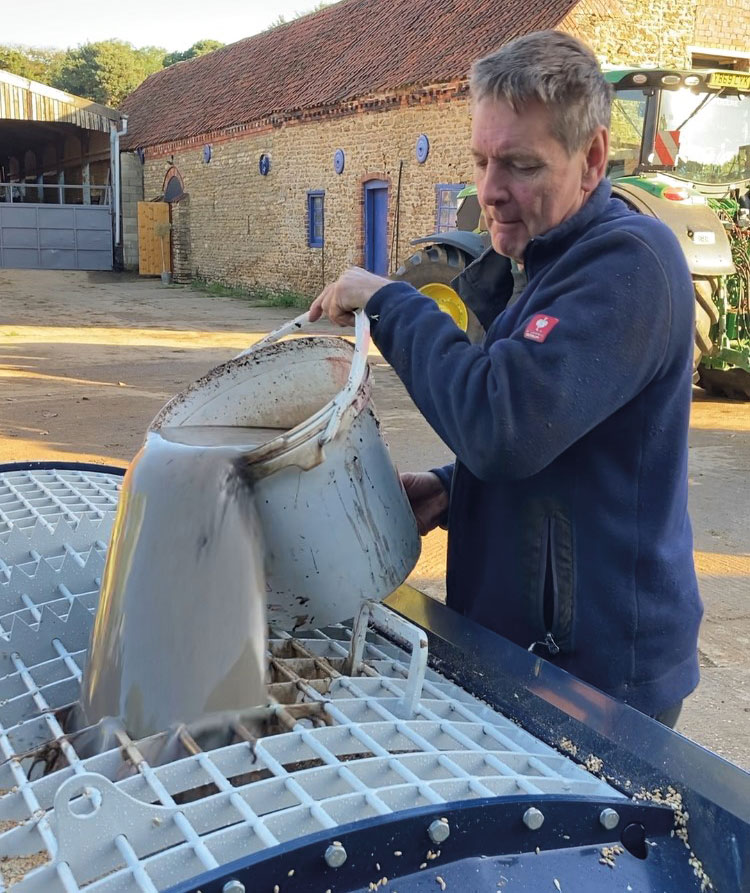
Andrew Jackson mixing the extract with the seed © Andrew Jackson
Rather than using an IBC, he found a local company to roll some mesh into a cylinder and used Terran fabric as its lining.
His raw material was primarily leaf mulch, although he added some farmyard manure to a second batch.
In hindsight he thinks he should have added some green material as the temperature didn’t rise at the beginning of the composting.
Composting worms, sourced from Yorkshire Worms were added, along with a sprinkler system that uses rainwater rather than tap water, as he is concerned chlorine in tap water might kill the microbes.
He found he needed to irrigate for about one minute each day to keep the compost at the required moisture content.
After a year, the finished compost had a peaty consistency, he says.
This was sieved and flushed with rainwater, with the resultant syrupy extract applied to four 0.5t batches of Skyscraper winter wheat using an Agritrend mixer bucket, along with molasses and milk, using a recipe he found online.
“This needs to be done on the day of drilling, which is a bit of a clash, as when you’re drilling you want to be getting on.
“But contrary to what many people might think, after mixing a load of water into seed we found it doesn’t affect flowability of the seed in the drill.”
His research suggests seed treatment is the most effective way on introducing the biology, followed by down the seed slot when drilling, and then overall spray application.
He drilled two fields with the treated seed this autumn. “At the moment the wheat doesn’t look much different to our other crops.”
One field was finished with some untreated Gleam, which in April was looking a slightly paler green, but he recognises that could be a varietal difference rather than due to the extract.
“It will be interesting to see the final yields,” he says.